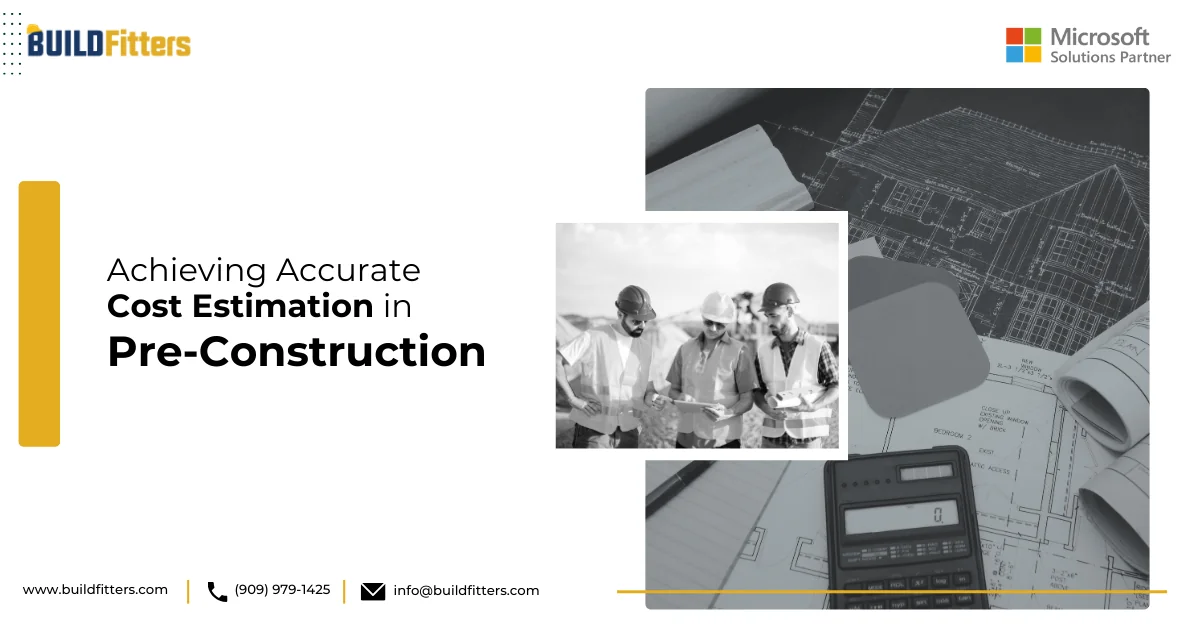
Achieving Accurate Cost Estimation in Pre-Construction
Introduction
Accurate cost estimation in the pre-construction phase is one of the most critical yet challenging tasks for professionals in the AEC (Architecture, Engineering, and Construction) industry. Project teams face intense pressure to deliver precise estimates quickly, as early-stage miscalculations can have ripple effects that lead to budget overruns, missed deadlines, and dissatisfied clients. Balancing speed with accuracy is no small feat, especially when project variables shift and market conditions fluctuate.
The importance of getting these numbers right cannot be overstated. According to McKinsey & Company, 80% of large construction projects go over budget, with inaccurate cost estimation cited as a major contributor. This statistic alone underscores the need for rigorous, data-driven approaches during the pre-construction phase, where even small miscalculations can escalate into costly issues down the line.
In this post, we’ll explore essential strategies to enhance the accuracy of cost estimations in pre-construction. From thorough planning and utilizing historical data to embracing advanced estimation software, these methods aim to minimize budget overruns and improve project profitability. This article is part of a broader series focused on integrating and simplifying pre-construction processes, laying the groundwork for streamlined estimation and budgeting.
The Role of Thorough Planning in Cost Estimation Accuracy
Accurate cost estimation in pre-construction begins with a thorough and detailed planning process. Without careful upfront planning, AEC professionals are left making guesses rather than informed decisions, increasing the likelihood of budget overruns and project delays. In pre-construction, where margins for error are slim, laying a strong foundation is essential for ensuring that all variables are considered before the first shovel hits the ground. By dedicating time to understanding the project’s full scope and involving key stakeholders early, companies can significantly improve the accuracy of their estimates.
Understanding the Scope of Work (SOW) for Accurate Cost Estimations:
A clear and comprehensive scope of work (SOW) is one of the most critical components for achieving accurate cost estimations in pre-construction. The SOW outlines all tasks, deliverables, materials, and timelines associated with a project, creating a roadmap that guides estimators in predicting the true cost. Without a well-defined scope, estimators are forced to make assumptions that can lead to mispricing materials, underestimating labor costs, or overlooking essential tasks altogether.
To avoid these pitfalls, it is essential to involve all key stakeholders early in the planning phase. This includes project managers, estimators, architects, subcontractors, and even clients. Collaborative input helps to ensure that no detail is overlooked, and each participant provides insights into the most cost-effective solutions based on their area of expertise. Early engagement of stakeholders leads to more accurate estimates, reducing the likelihood of costly revisions or scope changes later on.
The Impact of Poor Planning on Construction Budget Overruns:
Lack of thorough planning is one of the leading causes of budget overruns in construction projects. A study by the Construction Industry Institute found that poor scope definition is responsible for 20-25% of all project budget overruns. When planning is insufficient, estimators are more likely to overlook key cost drivers such as material price fluctuations, labor availability, or unforeseen site conditions.
One real-world example of this comes from a large-scale commercial project where poor scope definition and late-stage scope changes resulted in a 15% budget increase due to rework and unforeseen material costs. This is a common issue that affects many projects, particularly when early planning stages are rushed to meet aggressive timelines. By prioritizing detailed and thoughtful planning, AEC professionals can reduce the risks of cost overruns and ensure that project budgets are realistic and achievable.
Integrating Value Engineering in Pre-Construction Planning:
Another key strategy for improving cost estimation accuracy is the integration of value engineering during the pre-construction phase. Value engineering is a systematic approach that seeks to optimize project functions while minimizing costs. By assessing all aspects of the project’s design and execution, value engineering helps teams identify opportunities to reduce expenses without compromising on quality or performance.
Top-performing construction firms often implement continuous feedback loops from past projects to inform future cost estimates. These companies collect data on materials, labor, and logistical challenges to refine their planning accuracy for similar projects in the future. By incorporating lessons learned from previous jobs, teams can proactively identify areas where cost efficiencies can be achieved, improving both accuracy and profitability.
Incorporating value engineering early in the pre-construction process ensures that estimators are working with the most cost-effective solutions from the start. This approach leads to more accurate estimates, minimizes the need for costly changes mid-project, and enhances the overall profitability of the construction endeavor.
Leveraging Historical Data for More Accurate Estimations
One of the most powerful tools available to AEC professionals in the pre-construction phase is historical project data. By tapping into a company’s past projects, estimators can create more accurate and reliable cost projections for future work. Historical data offers a treasure trove of insights that enable construction firms to predict costs with greater precision, avoiding the pitfalls of underestimating resources or overlooking key cost drivers. In an industry where even small miscalculations can have significant consequences, leveraging past data is a game-changer for pre-construction cost estimation.
Building a Robust Database of Past Projects to Enhance Estimation Accuracy:
The foundation of any data-driven cost estimation strategy lies in building a comprehensive and well-organized database of past projects. Historical data provides a reliable benchmark for future estimates, as it reflects real-world conditions and outcomes. Tracking project-specific factors such as geographic location, material costs, labor rates, project size, and complexity allows estimators to identify patterns and trends that directly inform their predictions.
For example, material costs can vary significantly by region, while labor rates are influenced by local demand and availability. By maintaining detailed records of how these variables played out in previous projects, construction firms can fine-tune their estimates for similar future projects, accounting for regional differences and market fluctuations. This approach enables companies to set more realistic budgets, reducing the risk of cost overruns and ensuring that estimates are both competitive and profitable.
Case Study: Improving Estimate Accuracy with Historical Data
To illustrate the impact of using historical data, consider a large construction firm that made the shift from manual estimation methods to data-driven practices. By developing a robust database of past projects and tracking cost variations across materials, labor, and site conditions, this firm saw significant improvements in their estimation accuracy. According to Dodge Data & Analytics, firms that harnessed historical data for pre-construction estimates reported up to a 30% improvement in overall accuracy. This reduction in estimation errors not only resulted in fewer budget overruns but also enhanced client satisfaction and increased profitability across their projects.
Tired of outdated estimation methods?
BUILDFitters offers real-time data, advanced tools, and seamless collaboration to boost accuracy. Request a demo today and optimize your pre-construction process!
Utilizing Cost Escalation Models and Contingency Planning for Accurate Projections:
While historical data is an essential resource, it’s important to recognize that past costs don’t always directly translate to future conditions. Construction projects are subject to cost escalations due to a variety of factors, including inflation, material shortages, labor market fluctuations, and unforeseen site conditions. Therefore, integrating cost escalation models and contingency planning into your historical data analysis is crucial to ensure your estimates remain accurate even in volatile market conditions.
Cost escalation models help estimators account for changes in material prices and labor costs over time. For instance, steel prices can vary by 5-10% year over year due to shifts in global supply chains. By applying escalation factors to historical data, estimators can make necessary adjustments to project costs for future timelines.
Similarly, incorporating contingency allowances is a common industry practice to mitigate the risks of unforeseen expenses. The industry rule of thumb suggests that adding a contingency buffer of 5-10% to the project’s estimated cost can cover unexpected price fluctuations, changes in project scope, or delays that may arise. This proactive approach ensures that projects are less vulnerable to financial strain and maintains a healthy profit margin even when conditions shift.
Embracing Advanced Estimation Software for Enhanced Accuracy
In 2024’s fast-paced construction environment, relying on manual methods for pre-construction cost estimation is no longer feasible for firms that want to stay competitive. Modern estimation software has revolutionized the way AEC professionals approach this critical task, offering powerful tools that integrate automation, real-time data, and predictive analytics. By leveraging these technologies, firms can enhance the accuracy and efficiency of their cost estimates, ensuring that projects stay on budget and on schedule.
The Evolution of Estimation Tools: From Spreadsheets to AI and BIM
The shift from traditional, spreadsheet-based estimation to advanced digital tools marks a significant evolution in the pre-construction process. Building Information Modeling (BIM) and AI-powered estimation platforms are at the forefront of this transformation, providing a level of precision and speed that was previously unattainable. These technologies enable estimators to create highly detailed, data-driven cost models that factor in real-time variables such as material prices, labor rates, and project specifications.
BIM, in particular, allows for a 3D representation of the project that integrates design, scheduling, and cost estimation in one seamless process. This holistic approach not only improves accuracy but also reduces the time it takes to generate estimates by automating many of the calculations and data entry tasks that were once performed manually. Meanwhile, AI-powered estimation tools use machine learning to analyze historical data and predict future costs with greater precision, adapting to changing market conditions and project variables as new data becomes available.
Benefits of Cloud-Based Estimation Platforms for Pre-Construction:
The adoption of cloud-based estimation platforms has further enhanced the efficiency and accuracy of pre-construction cost estimation. These platforms offer real-time collaboration among team members, regardless of location, allowing project managers, estimators, architects, and subcontractors to work together seamlessly on the same platform. This collaborative environment reduces the likelihood of miscommunication, minimizes manual errors, and ensures that all team members are working from the most up-to-date information.
Additionally, cloud-based platforms allow for quick revisions and updates to estimates as project scopes change or new market data becomes available. For example, if material costs suddenly increase due to supply chain disruptions, the platform can immediately update the cost estimate, ensuring that it remains accurate and reflective of current conditions.
A study conducted by the National Institute of Standards and Technology (NIST) found that contractors using BIM saw overall cost reductions of 3-5%. These savings were attributed to improved coordination, reduced rework, and fewer costly errors during the estimation and construction phases. Cloud-based tools, when combined with BIM, further amplify these benefits by allowing teams to work dynamically, adjusting estimates in real-time as new data or design changes arise.
Case in Point: BUILDFitter’s Approach to Collaborative Estimation
Platforms like BUILDFitters make collaborative estimation processes seamless, ensuring that all stakeholders stay aligned from the outset of the project.
Real-Time Data for Dynamic Adjustments and Accurate Forecasting:
One of the most significant advantages of advanced estimation software is the ability to work with real-time data. Unlike static estimation methods, which are quickly outdated as market conditions shift, modern software solutions continuously pull in updated information on material costs, labor rates, and other critical factors. This allows estimators to make dynamic adjustments throughout the pre-construction phase, ensuring that estimates remain accurate as the project evolves.
For instance, a project that spans several months may experience fluctuations in material prices due to economic factors or supply chain constraints. With real-time data integration, estimators can adjust the project budget accordingly, reducing the risk of cost overruns. Additionally, these tools often come equipped with predictive analytics that provide forecasts based on historical trends, helping firms anticipate potential cost escalations or bottlenecks before they occur.
Collaborative Estimation Processes for Stakeholder Alignment
Collaboration is key to achieving accurate and reliable cost estimations in pre-construction. Involving all project stakeholders early on ensures that everyone is on the same page, reducing the chances of estimation discrepancies, budget overruns, or misunderstandings as the project progresses. By fostering transparency and open communication among teams, companies can avoid costly rework and deliver more precise estimates that meet client expectations.
Cross-Functional Collaboration in Pre-Construction:
Pre-construction cost estimation is not a task that should fall solely on the shoulders of estimators. To ensure accuracy, it requires cross-functional collaboration between various stakeholders, including architects, engineers, contractors, and project managers. Each team brings its own expertise to the table, offering insights into design considerations, material specifications, and construction methods that can directly impact costs.
When all key stakeholders are aligned early in the pre-construction phase, the project benefits from collective input, which helps identify potential cost drivers and risks that could otherwise be overlooked. This collaborative approach promotes transparency and ensures that each party has visibility into the decision-making process, which reduces the likelihood of discrepancies in cost estimates. Additionally, having all teams involved from the start can streamline the project timeline, as decisions are made with a holistic understanding of the project’s goals, constraints, and resources.
Client Education and Expectation Setting:
While internal collaboration is vital, equally important is educating clients on the estimation process. Often, clients may not fully understand the complexities involved in pre-construction cost estimation, leading to unrealistic expectations regarding project costs and timelines. By clearly communicating the risks, contingencies, and potential cost escalations that can arise throughout the project, AEC professionals can set more realistic expectations and build trust with their clients.
Clients should be informed about the importance of contingency planning and the inclusion of buffers for unforeseen expenses, such as material price fluctuations or scope changes. Discussing potential risks early in the process, and explaining how these factors are accounted for in the estimates, ensures there are no surprises later on. This transparency not only improves the client relationship but also protects the project from disputes over budget changes or delays. When clients understand the logic behind the estimates, they are more likely to support necessary adjustments as the project evolves.
Streamline your Pre-Construction Cost Estimation Process
Request a demo of BUILDFitters today to explore how our platform enhances collaboration, improves accuracy, and supports more efficient project management.
Measuring and Monitoring Estimation Accuracy
Accurate pre-construction cost estimation doesn’t end once the project is underway. For AEC professionals to consistently deliver successful projects, it’s essential to track the performance of their estimates and refine their processes over time. By measuring key performance indicators (KPIs) and implementing continuous feedback loops, construction firms can not only enhance their estimation accuracy but also improve overall project profitability.
Key Metrics to Track in Pre-Construction Estimation:
To effectively monitor the accuracy of pre-construction cost estimates, AEC firms need to focus on specific Key Performance Indicators (KPIs) that reflect both cost and schedule performance. Two of the most widely used metrics for this purpose are the Cost Performance Index (CPI) and the Schedule Performance Index (SPI).
- Cost Performance Index (CPI): CPI measures the efficiency of project spending by comparing the actual costs incurred with the estimated costs. A CPI value above 1.0 indicates that a project is running under budget, while a value below 1.0 suggests that the project is exceeding its budget. Tracking CPI helps project managers assess the accuracy of the initial cost estimation and make adjustments as needed.
- Schedule Performance Index (SPI): SPI evaluates whether a project is progressing according to its planned schedule. An SPI greater than 1.0 means the project is ahead of schedule, while a value below 1.0 indicates delays. Monitoring SPI allows teams to identify discrepancies between the planned and actual timelines, helping them adjust forecasts and resource allocation to stay on track.
In addition to CPI and SPI, other metrics such as variance at completion (VAC)—which measures the anticipated cost variance at the end of the project—and earned value (EV) can provide further insight into the accuracy of pre-construction estimates. These metrics offer AEC professionals a comprehensive view of project performance, allowing them to make data-driven decisions that mitigate risks and improve outcomes.
Moreover, performing post-project evaluations is critical for understanding where estimations succeeded or fell short. By analyzing the differences between the estimated and actual costs and timelines, firms can identify patterns, correct inaccurate assumptions, and refine their processes for future projects. This reflection helps improve the accuracy of future estimates, ensuring that each project benefits from the lessons learned on previous jobs.
Continuous Improvement Through Feedback Loops:
Top-performing construction firms don’t just rely on past estimates—they continuously improve them by integrating feedback loops into their pre-construction processes. A feedback loop involves analyzing the outcomes of completed projects to adjust estimation models for future work. This approach allows firms to build on their past successes and avoid repeating previous mistakes.
For instance, if a particular type of project consistently exceeds its estimated costs due to labor shortages or material price increases, firms can adjust their estimation models to better account for these factors. Additionally, feedback from field teams about unforeseen conditions or inefficiencies during construction can inform more realistic estimates moving forward.
By incorporating these insights, construction firms can develop more accurate cost models that reflect real-world conditions. This iterative process not only improves cost estimation accuracy but also enhances long-term profitability by reducing the risk of budget overruns and ensuring that projects are completed within the allocated time and resources.
Conclusion
Accurate pre-construction cost estimation is the foundation of a successful project, and achieving this accuracy requires a strategic approach. Thorough planning, leveraging historical data, adopting advanced estimation software, and fostering collaboration among stakeholders are essential practices for reducing the risk of budget overruns and ensuring project profitability. By integrating these key elements, AEC professionals can improve the reliability of their estimates and deliver better outcomes for their clients.
In the next article of this series, we’ll explore how BUILDFitters simplifies the entire estimation and budgeting process. From streamlining collaboration to automating cost tracking, BUILDFitters provides a seamless solution to the common challenges faced in pre-construction.
For now, be sure to check out our related article on integrating estimation and budgeting to see how these processes work hand-in-hand. Stay tuned for more insights on how BUILDFitters can transform your pre-construction workflow.